জল প্রতিরোধ ক্ষমতা কম, অসম পৃষ্ঠ, উচ্চ পাউডারের পরিমাণ এবং অসম দৈর্ঘ্য? জলজ খাদ্য উৎপাদনে সাধারণ সমস্যা এবং উন্নতির ব্যবস্থা
আমাদের প্রতিদিনের জলজ খাদ্য উৎপাদনে, আমরা বিভিন্ন দিক থেকে কিছু সমস্যার সম্মুখীন হয়েছি। এখানে সবার সাথে আলোচনা করার জন্য কিছু উদাহরণ দেওয়া হল, যেমন:
১, সূত্র
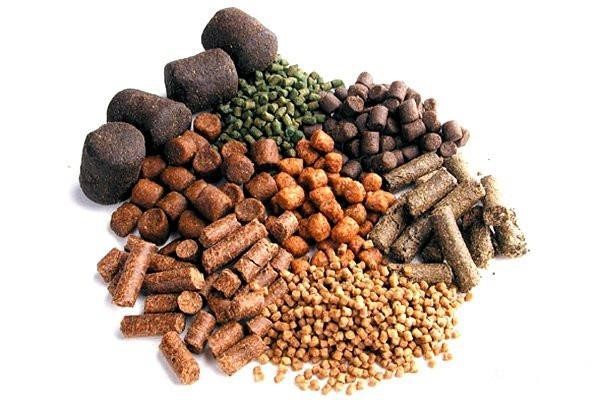
১. মাছের খাদ্যের সূত্র কাঠামোতে, আরও ধরণের খাবারের কাঁচামাল থাকে, যেমন রেপসিড খাবার, তুলার খাবার ইত্যাদি, যা অপরিশোধিত আঁশের অন্তর্গত। কিছু তেল কারখানায় উন্নত প্রযুক্তি রয়েছে এবং তেলটি মূলত খুব কম পরিমাণে শুকিয়ে ভাজা হয়। তাছাড়া, এই ধরণের কাঁচামাল উৎপাদনে সহজে শোষিত হয় না, যা দানাদারকরণের উপর অনেক প্রভাব ফেলে। এছাড়াও, তুলার খাবার চূর্ণ করা কঠিন, যা দক্ষতাকে প্রভাবিত করে।
২. সমাধান: রেপসিড কেকের ব্যবহার বৃদ্ধি করা হয়েছে, এবং উচ্চমানের স্থানীয় উপাদান যেমন চালের ভুসি যোগ করা হয়েছে। অতিরিক্তভাবে, গম, যা সূত্রের প্রায় ৫-৮%, যোগ করা হয়েছে। সমন্বয়ের মাধ্যমে, ২০০৯ সালে দানাদার প্রভাব তুলনামূলকভাবে আদর্শ, এবং প্রতি টন ফলনও বৃদ্ধি পেয়েছে। ২.৫ মিমি কণা ৮-৯ টনের মধ্যে, যা অতীতের তুলনায় প্রায় ২ টন বৃদ্ধি পেয়েছে। কণাগুলির চেহারাও উল্লেখযোগ্যভাবে উন্নত হয়েছে।
এছাড়াও, তুলাবীজ গুঁড়ো করার দক্ষতা উন্নত করার জন্য, আমরা তুলাবীজ গুঁড়ো এবং র্যাপসিড গুঁড়ো ২:১ অনুপাতে মিশিয়েছিলাম, তারপর গুঁড়ো করার গতি মূলত র্যাপসিড গুঁড়ো করার গতির সমান ছিল।
২, কণার অসম পৃষ্ঠ
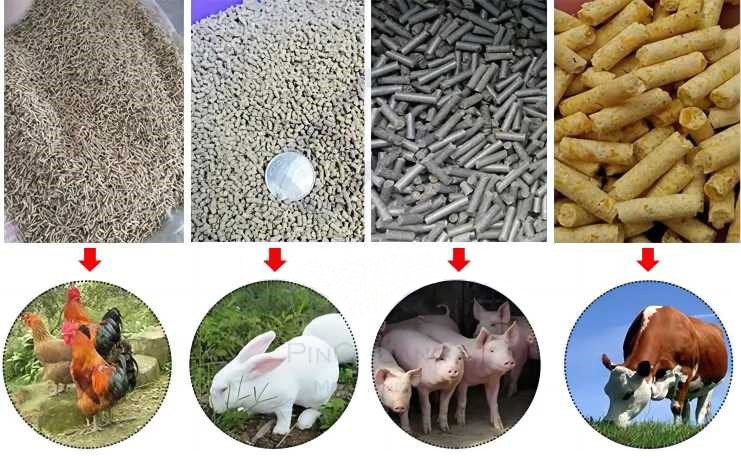
১. এটি তৈরি পণ্যের চেহারার উপর বিরাট প্রভাব ফেলে এবং পানিতে যোগ করলে এটি ভেঙে যাওয়ার প্রবণতা থাকে এবং এর ব্যবহারের হার কম থাকে। এর প্রধান কারণ হল:
(১) কাঁচামালগুলি খুব মোটা করে চূর্ণ করা হয়, এবং টেম্পারিং প্রক্রিয়ার সময়, এগুলি সম্পূর্ণরূপে পরিপক্ক এবং নরম হয় না, এবং ছাঁচের গর্তের মধ্য দিয়ে যাওয়ার সময় অন্যান্য কাঁচামালের সাথে ভালভাবে মিলিত হতে পারে না।
(২) উচ্চ পরিমাণে অপরিশোধিত ফাইবারযুক্ত ফিশ ফিড ফর্মুলায়, টেম্পারিং প্রক্রিয়ার সময় কাঁচামালে বাষ্পীয় বুদবুদের উপস্থিতির কারণে, কণা সংকোচনের সময় ছাঁচের ভিতরে এবং বাইরে চাপের পার্থক্যের কারণে এই বুদবুদগুলি ফেটে যায়, যার ফলে কণাগুলির পৃষ্ঠ অসম হয়।
2. পরিচালনার ব্যবস্থা:
(১) পেষণ প্রক্রিয়া সঠিকভাবে নিয়ন্ত্রণ করুন
বর্তমানে, মাছের খাবার উৎপাদনের সময়, আমাদের কোম্পানি বাল্ক কাঁচামাল হিসেবে ১.২ মিমি চালনী মাইক্রো পাউডার ব্যবহার করে। আমরা চালনী ব্যবহারের ফ্রিকোয়েন্সি এবং হাতুড়ির ক্ষয়ক্ষতির মাত্রা নিয়ন্ত্রণ করি যাতে পেষণের সূক্ষ্মতা নিশ্চিত করা যায়।
(২) বাষ্পের চাপ নিয়ন্ত্রণ করুন
সূত্র অনুসারে, উৎপাদনের সময় বাষ্পের চাপ যুক্তিসঙ্গতভাবে সামঞ্জস্য করুন, সাধারণত 0.2 এর কাছাকাছি নিয়ন্ত্রণ করুন। মাছের খাদ্য সূত্রে প্রচুর পরিমাণে মোটা ফাইবার কাঁচামাল থাকার কারণে, উচ্চমানের বাষ্প এবং যুক্তিসঙ্গত টেম্পারিং সময় প্রয়োজন।
৩, কণার দুর্বল জল প্রতিরোধ ক্ষমতা
১. এই ধরণের সমস্যা আমাদের দৈনন্দিন উৎপাদনে সবচেয়ে সাধারণ, সাধারণত নিম্নলিখিত কারণগুলির সাথে সম্পর্কিত:
(১) স্বল্প টেম্পারিং সময় এবং কম টেম্পারিং তাপমাত্রার ফলে অসম বা অপর্যাপ্ত টেম্পারিং, কম পাকা ডিগ্রী এবং অপর্যাপ্ত আর্দ্রতা দেখা দেয়।
(২) স্টার্চের মতো অপর্যাপ্ত আঠালো উপাদান।
(3) রিং মোল্ডের কম্প্রেশন অনুপাত খুব কম।
(৪) সূত্রে তেলের পরিমাণ এবং অপরিশোধিত ফাইবারের কাঁচামালের অনুপাত অত্যধিক।
(৫) কণার আকারের গুণক ক্রাশ করা।
2. পরিচালনার ব্যবস্থা:
(১) বাষ্পের মান উন্নত করুন, নিয়ন্ত্রকের ব্লেড কোণ সামঞ্জস্য করুন, টেম্পারিং সময় বাড়ান এবং কাঁচামালের আর্দ্রতা যথাযথভাবে বৃদ্ধি করুন।
(২) সূত্রটি সামঞ্জস্য করুন, যথাযথভাবে স্টার্চ কাঁচামাল বৃদ্ধি করুন এবং চর্বি এবং অপরিশোধিত ফাইবার কাঁচামালের অনুপাত হ্রাস করুন।
(৩) প্রয়োজনে আঠালো যোগ করুন। (সোডিয়াম ভিত্তিক বেন্টোনাইট স্লারি)
(৪) এর সংকোচন অনুপাত উন্নত করুনরিং ডাই
(৫) কূপ পেষণের সূক্ষ্মতা নিয়ন্ত্রণ করুন
৪, কণায় অতিরিক্ত পাউডারের পরিমাণ
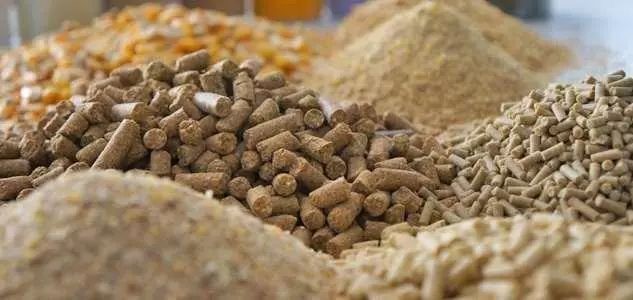
১. ঠান্ডা করার পরে এবং স্ক্রিনিংয়ের আগে সাধারণ পেলেট ফিডের উপস্থিতি নিশ্চিত করা কঠিন। গ্রাহকরা জানিয়েছেন যে পেলেটে আরও সূক্ষ্ম ছাই এবং গুঁড়ো রয়েছে। উপরের বিশ্লেষণের ভিত্তিতে, আমি মনে করি এর বেশ কয়েকটি কারণ রয়েছে:
উ: কণার পৃষ্ঠ মসৃণ নয়, ছেদন স্থানটি পরিষ্কার নয়, এবং কণাগুলি আলগা এবং পাউডার তৈরির প্রবণতা রয়েছে;
খ. স্ক্রিন গ্রেডিং করে অসম্পূর্ণ স্ক্রিনিং, স্ক্রিন জাল আটকে যাওয়া, রাবার বলের তীব্র ক্ষয়, স্ক্রিন জালের অ্যাপারচারের অমিল ইত্যাদি;
গ. সমাপ্ত পণ্যের গুদামে প্রচুর পরিমাণে সূক্ষ্ম ছাইয়ের অবশিষ্টাংশ রয়েছে এবং পরিষ্কারের কাজটি পুঙ্খানুপুঙ্খভাবে সম্পন্ন হয়নি;
ঘ. প্যাকেজিং এবং ওজন করার সময় ধুলো অপসারণের কিছু গোপন বিপদ রয়েছে;
পরিচালনার ব্যবস্থা:
উ: সূত্রের কাঠামোটি অপ্টিমাইজ করুন, যুক্তিসঙ্গতভাবে রিং ডাই নির্বাচন করুন এবং কম্প্রেশন অনুপাতটি ভালভাবে নিয়ন্ত্রণ করুন।
খ. দানাদার প্রক্রিয়া চলাকালীন, কাঁচামাল সম্পূর্ণরূপে পাকা এবং নরম করার জন্য টেম্পারিং সময়, খাওয়ানোর পরিমাণ এবং দানাদার তাপমাত্রা নিয়ন্ত্রণ করুন।
গ. নিশ্চিত করুন যে কণার ক্রস-সেকশনটি পরিষ্কার এবং স্টিলের স্ট্রিপ দিয়ে তৈরি নরম কাটার ছুরি ব্যবহার করুন।
ঘ. গ্রেডিং স্ক্রিনটি সামঞ্জস্য করুন এবং রক্ষণাবেক্ষণ করুন, এবং একটি যুক্তিসঙ্গত স্ক্রিন কনফিগারেশন ব্যবহার করুন।
E. সমাপ্ত পণ্য গুদামের অধীনে সেকেন্ডারি স্ক্রিনিং প্রযুক্তির ব্যবহার পাউডার সামগ্রীর অনুপাতকে ব্যাপকভাবে হ্রাস করতে পারে।
F. সমাপ্ত পণ্যের গুদাম এবং সার্কিট সময়মতো পরিষ্কার করা প্রয়োজন। এছাড়াও, প্যাকেজিং এবং ধুলো অপসারণ ডিভাইস উন্নত করা প্রয়োজন। ধুলো অপসারণের জন্য নেতিবাচক চাপ ব্যবহার করা ভাল, যা আরও আদর্শ। বিশেষ করে প্যাকেজিং প্রক্রিয়ার সময়, প্যাকেজিং কর্মীর নিয়মিতভাবে প্যাকেজিং স্কেলের বাফার হপার থেকে ধুলো ঠেলে পরিষ্কার করা উচিত।.
৫, কণার দৈর্ঘ্য পরিবর্তিত হয়
১. দৈনন্দিন উৎপাদনে, আমরা প্রায়শই নিয়ন্ত্রণে অসুবিধার সম্মুখীন হই, বিশেষ করে ৪২০ এর উপরে মডেলগুলির ক্ষেত্রে। এর কারণগুলি মোটামুটিভাবে নিম্নরূপ:
(১) দানাদারকরণের জন্য খাওয়ানোর পরিমাণ অসম, এবং টেম্পারিং প্রভাব ব্যাপকভাবে ওঠানামা করে।
(২) ছাঁচ রোলারগুলির মধ্যে অসঙ্গতিপূর্ণ ফাঁক অথবা রিং ছাঁচ এবং চাপ রোলারগুলির তীব্র ক্ষয়।
(৩) রিং মোল্ডের অক্ষীয় দিক বরাবর, উভয় প্রান্তে স্রাবের গতি মাঝখানের চেয়ে কম।
(৪) রিং মোল্ডের চাপ কমানোর গর্তটি খুব বড় এবং খোলার হার খুব বেশি।
(৫) কাটিং ব্লেডের অবস্থান এবং কোণ অযৌক্তিক।
(6) দানাদার তাপমাত্রা।
(৭) রিং ডাই কাটিং ব্লেডের ধরণ এবং কার্যকর উচ্চতা (ব্লেডের প্রস্থ, প্রস্থ) এর উপর প্রভাব পড়ে।
(8) একই সময়ে, কম্প্রেশন চেম্বারের ভিতরে কাঁচামালের বন্টন অসম।
২. খাদ্য এবং পেলেটের গুণমান সাধারণত তাদের অভ্যন্তরীণ এবং বাহ্যিক গুণাবলীর উপর ভিত্তি করে বিশ্লেষণ করা হয়। উৎপাদন ব্যবস্থা হিসাবে, আমরা খাদ্য পেলেটের বাহ্যিক গুণমানের সাথে সম্পর্কিত বিষয়গুলির সাথে বেশি পরিচিত। উৎপাদন দৃষ্টিকোণ থেকে, জলজ খাদ্য পেলেটের গুণমানকে প্রভাবিত করে এমন কারণগুলিকে মোটামুটিভাবে নিম্নরূপে সংক্ষেপিত করা যেতে পারে:
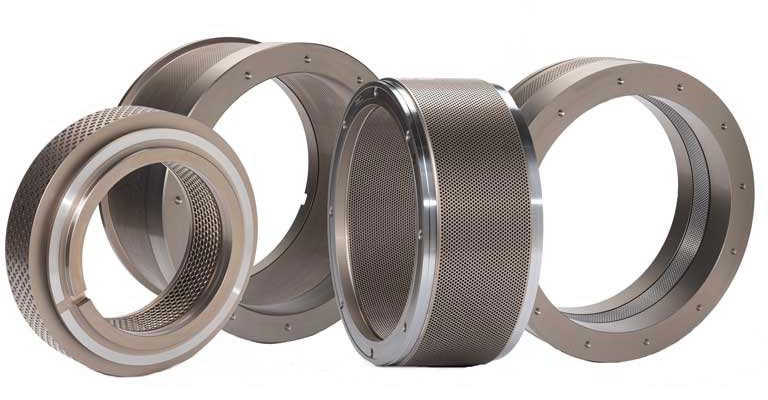
(১) সূত্রের নকশা এবং সংগঠন জলজ খাদ্য পেলেটের মানের উপর সরাসরি প্রভাব ফেলে, যা মোটের প্রায় ৪০%;
(২) চূর্ণ করার তীব্রতা এবং কণার আকারের অভিন্নতা;
(৩) রিং মোল্ডের ব্যাস, সংকোচন অনুপাত এবং রৈখিক বেগ কণার দৈর্ঘ্য এবং ব্যাসের উপর প্রভাব ফেলে;
(৪) রিং মোল্ডের কম্প্রেশন অনুপাত, রৈখিক বেগ, নিভানোর এবং টেম্পারিং প্রভাব এবং কণার দৈর্ঘ্যের উপর কাটিং ব্লেডের প্রভাব;
(৫) কাঁচামালের আর্দ্রতা, টেম্পারিং প্রভাব, শীতলকরণ এবং শুকানোর ফলে সমাপ্ত পণ্যের আর্দ্রতা এবং চেহারার উপর প্রভাব পড়ে;
(৬) যন্ত্র নিজেই, প্রক্রিয়াজাতকরণের কারণগুলি, এবং নিভানোর এবং টেম্পারিং প্রভাবগুলি কণার পাউডারের পরিমাণের উপর প্রভাব ফেলে;
৩. পরিচালনার ব্যবস্থা:
(১) ফ্যাব্রিক স্ক্র্যাপারের দৈর্ঘ্য, প্রস্থ এবং কোণ সামঞ্জস্য করুন এবং জীর্ণ স্ক্র্যাপটি প্রতিস্থাপন করুন।
(২) কম খাওয়ানোর পরিমাণের কারণে উৎপাদনের শুরুতে এবং শেষের দিকে সময়মতো কাটিং ব্লেডের অবস্থান সামঞ্জস্য করার দিকে মনোযোগ দিন।
(৩) উৎপাদন প্রক্রিয়া চলাকালীন, স্থিতিশীল খাওয়ানোর হার এবং বাষ্প সরবরাহ নিশ্চিত করুন। যদি বাষ্পের চাপ কম থাকে এবং তাপমাত্রা বাড়তে না পারে, তাহলে সময়মতো এটি সামঞ্জস্য করা বা বন্ধ করা উচিত।
(৪) যুক্তিসঙ্গতভাবে এর মধ্যে ব্যবধান সামঞ্জস্য করুনরোলার শেলনতুন ছাঁচে নতুন রোলার লাগান এবং ক্ষয়ের কারণে চাপ রোলার এবং রিং ছাঁচের অসম পৃষ্ঠটি দ্রুত মেরামত করুন।
(৫) রিং মোল্ডের গাইড হোলটি মেরামত করুন এবং ব্লক করা মোল্ড হোলটি দ্রুত পরিষ্কার করুন।
(৬) রিং মোল্ড অর্ডার করার সময়, মূল রিং মোল্ডের অক্ষীয় দিকের উভয় প্রান্তে থাকা তিনটি সারির গর্তের সংকোচন অনুপাত মাঝখানের তুলনায় ১-২ মিমি ছোট হতে পারে।
(৭) একটি নরম কাটার ছুরি ব্যবহার করুন, যার পুরুত্ব ০.৫-১ মিমি এর মধ্যে নিয়ন্ত্রিত, যাতে যতটা সম্ভব ধারালো ধার নিশ্চিত করা যায়, যাতে এটি রিং মোল্ড এবং প্রেসার রোলারের মধ্যে জাল লাইনে থাকে।
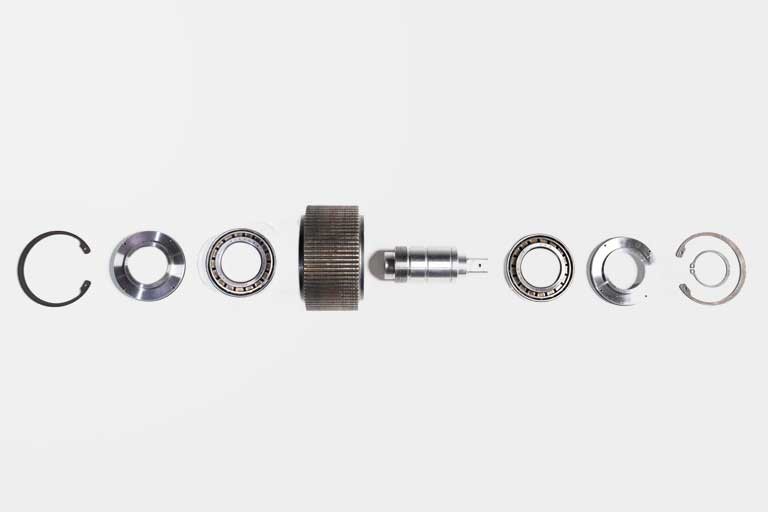
(৮) রিং মোল্ডের ঘনত্ব নিশ্চিত করুন, নিয়মিতভাবে গ্রানুলেটরের স্পিন্ডেল ক্লিয়ারেন্স পরীক্ষা করুন এবং প্রয়োজনে এটি সামঞ্জস্য করুন।
৬, সারাংশ নিয়ন্ত্রণ পয়েন্ট:
১. গ্রাইন্ডিং: স্পেসিফিকেশনের প্রয়োজনীয়তা অনুসারে গ্রাইন্ডিংয়ের সূক্ষ্মতা নিয়ন্ত্রণ করতে হবে।
২. মিশ্রণ: কাঁচামাল মিশ্রণের অভিন্নতা নিয়ন্ত্রণ করতে হবে যাতে মিশ্রণের পরিমাণ, মিশ্রণের সময়, আর্দ্রতার পরিমাণ এবং তাপমাত্রা যথাযথভাবে নিশ্চিত করা যায়।
৩. পরিপক্কতা: পাফিং মেশিনের চাপ, তাপমাত্রা এবং আর্দ্রতা নিয়ন্ত্রণ করতে হবে।
কণা উপাদানের আকার এবং আকৃতি: কম্প্রেশন ছাঁচ এবং কাটিং ব্লেডের উপযুক্ত স্পেসিফিকেশন নির্বাচন করতে হবে।
৫. প্রস্তুত খাদ্যের পানির পরিমাণ: শুকানোর এবং ঠান্ডা করার সময় এবং তাপমাত্রা নিশ্চিত করা প্রয়োজন।
৬. তেল স্প্রে: তেল স্প্রে করার সঠিক পরিমাণ, নোজেলের সংখ্যা এবং তেলের গুণমান নিয়ন্ত্রণ করা প্রয়োজন।
৭. স্ক্রিনিং: উপাদানের স্পেসিফিকেশন অনুসারে চালুনির আকার নির্বাচন করুন।
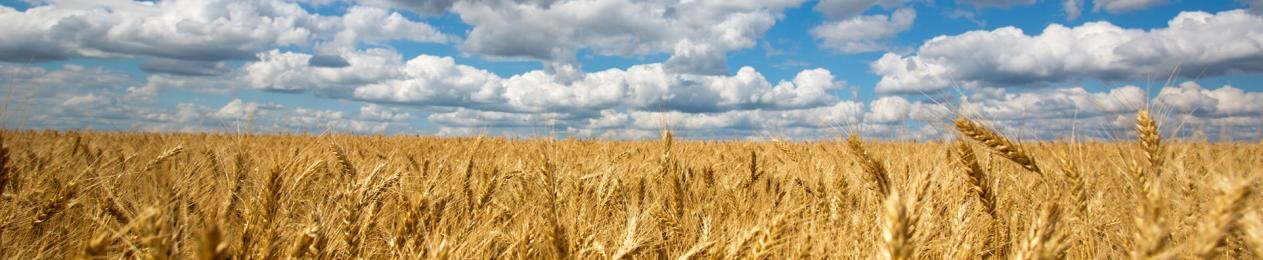
পোস্টের সময়: নভেম্বর-৩০-২০২৩